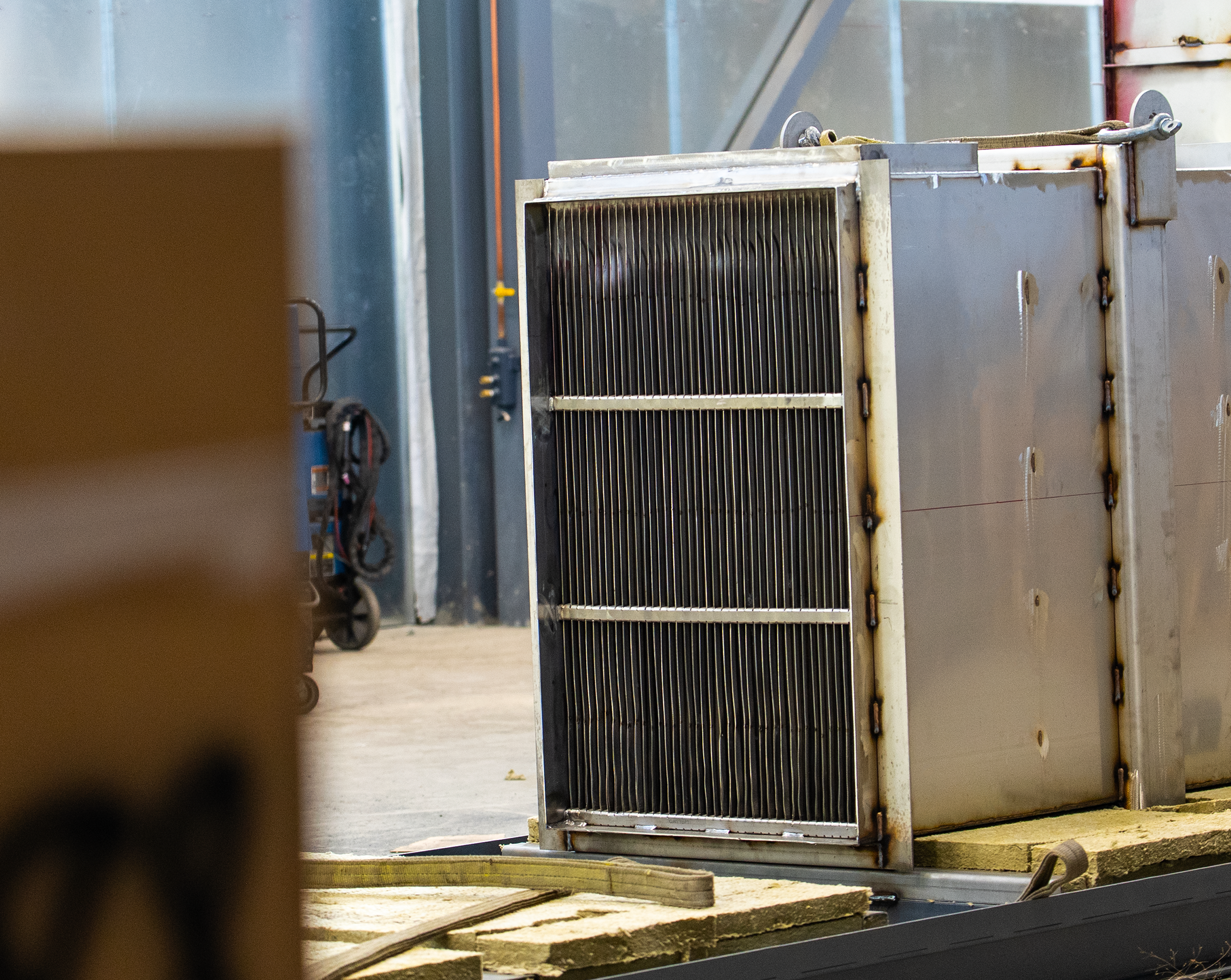
Throughout the industrial world, cost savings is the name of the game. Manufacturers are always looking for new ways to lower their overhead without sacrificing on the quality of their final product.
There’s one proven solution that many factory owners still haven’t heard about – air-to-air heat recovery units. In this blog, we’ll explain what heat exchangers are, how they work, and their unique benefits.
What Is an Air-to-Air Heat Exchanger?
Simply put, air-to-air heat recovery units recapture waste heat that is emitted during the manufacturing process, and recycle it back into other areas of assembly that require heated air. This results in significant energy savings. It’s an effective and efficient solution for all types of manufacturing.
There are a couple different ways to put air-to-air heat recovery units to work. In the most direct application, air-to-air heat recovery units take in exhausted air from a given area in the industrial process and funnel it directly into another part of the process that needs heated air.
Additionally, after capturing exhausted heat, a heat recovery unit can run this air through a tube while also taking in new air from the outside. The unit runs the outside air in a tube that passes over the exhausted air, which preheats it for use in the factory. All of this happens without mixing the air streams, so there is never a risk of the exhaust air contaminating the incoming air.
Benefits of Air-to-Air Heat Exchangers
By recapturing and reusing this air, manufacturers will see a significant return on investment with long-term use and a decrease in the amount of energy used at their facility, which will, in turn, result in a noticeable decrease in their energy bills.
Air-to-air units can also aid in the mitigation of airborne particulates and fumes, since they keep the exchanged air totally separate from the surrounding air. Heat recovery units also include a system of sleeves, grills, and filters that pre-filter the interior air. If your workplace deals with volatile organic compounds (VOCs), fumes, toxins, or pollutants, installing a heat recovery unit is an excellent way to help control and minimize them.
Types of Heat Exchangers
All heat recovery units have the same basic design of a vertically or horizontally stacked core that consists of a series of plates. Other commonalities include a handful of key characteristics:
- Affordable
- Lightweight
- Noise absorption capability
- Excellent thermal conduction
- Highly corrosion resistant
Beyond that, the designs of heat recovery units begin to diverge. Another benefit of air-to-air heat recovery systems is their flexibility to fit many different manufacturing facilities and industries. There are three common types: the dimpled plate (DPL) heat exchanger, the shell and tube heat exchanger, and the cooling tower.
The DPL is a versatile, rugged, heavy-duty, and easily cleanable plate heat exchanger. Its dimpled design ensures consistent plate spacing and enhanced turbulence while maintaining low-pressure drops. The all-welded construction prevents cross-contamination between gas streams. DPLs are most commonly used in manufacturing facilities that incorporate chemical processing, closed-loop to open-loop water cooling, cryogenics, food processing, and furnaces.
The shell and tube design contains cooling towers with large tube diameters that cool air streams with large amounts of particles. These towers help air control equipment to function more efficiently, and they recover heat that can be reused as building make-up air. Shell and tube units are most commonly used in factories that use boiler blowdown heat recovery, industrial paint systems, oil refining and cooling, preheating, steam generation, and vapor recovery systems.
The cooling tower is a vertical shell and tube heat exchanger with larger tube diameters that are designed for cooling air streams with large amounts of particulates before it enters a bag house for final cleaning and discharge into the atmosphere. Hot, dirty air enters the top of the unit and goes down through the tubes. Most of the particulates fall through the tubes and are collected underneath the exchanger in a large material collection hopper. Cooling towers are often used in facilities that contain any oven, dryer, kiln cupola, or incinerator with a particulate exhaust emission that needs to be cooled or dried out before going into a more temperature-sensitive collection device, food and feed dryers, mineral dryers, silicone thermal incinerators, solid waste incinerators, metal chip dryers and incinerators, and high-temperature kilns for curing materials.
Air-to-Air Innovation at PRE-heat
Air-to-air heat recovery units clearly have a lot to offer in virtually all areas of manufacturing. As the industry leader in air-to-air solutions, PRE-heat has been providing the highest quality air-to-air heat recovery units for over 40 years. PRE-heat’s knowledge of the industry has driven us to where we are today, creating improved shell and tube designs and improved plate designs all in-house. See how we tackle a project with innovative designs and efficient processes to get orders delivered exactly when they are needed. Contact PRE-heat today to start your air-to-air heat recovery project.