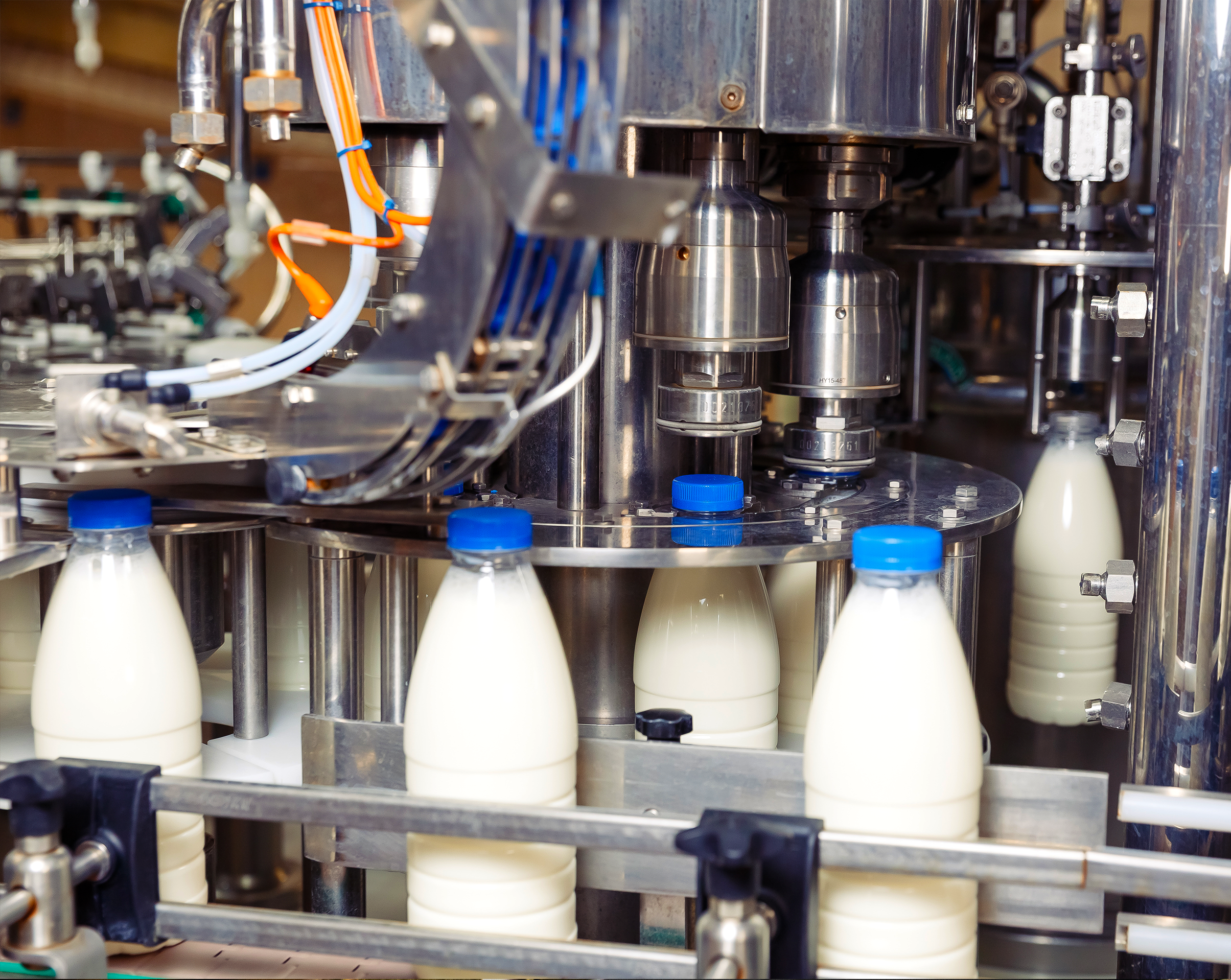
From raw ingredients to food packaging, there are myriad stringent processes and technologies in place throughout every step of the food production industry to make sure that the foods and drinks we consume every day are safe. As food industry professionals, it is our responsibility to ensure that we are always incorporating the best possible methods to improve the safety and quality of our products – after all, foods and beverages are quite literally a life or death matter.
Food Industry Needs for Temperature Regulation
Food production facilities often require precise temperature control over long periods of time. Specific temperatures are needed to be reached and maintained for vital processes like pasteurization, refrigeration, freezing, and sterilization – just to name a few. And these can all change based on the specific ingredients used.
Case in point: the FDA’s frequently updated Code of Federal Regulations Title 21 lays out a detailed account – nearly 1,800 words as of August 2024 – of demands and best practices for temperature controls at food processing facilities to prevent dangerous outcomes like microorganisms.
Air-to-air heat exchangers are a proven effective and reliable source for temperature control in food processing. Heat recovery units recapture the waste air that is emitted during food processing and reuse it in other parts of the process to maintain those precise temperature requirements.
The Air-to-Air Difference
Heat is one of the greatest sources of wasted energy in manufacturing. Typically, this heated air is vented out into the surrounding environment. Air-to-air heat recovery providers see this waste air as an opportunity, not a mere byproduct. Air-to-air heat exchanger units recapture and recycle air that would have gone to waste, delivering an efficient and economical solution for manufacturers.
There are a number of types of air-to-air heat recovery units to best fit the needs of various food production facilities.
The most commonly used style of heat recovery system in food processing is called dimpled plate (DPL) heat exchanger. The DPL is a versatile, rugged, heavy-duty, and easily cleanable plate heat exchanger. Its dimpled design ensures consistent plate spacing and enhanced turbulence while maintaining low-pressure drops. The all-welded construction prevents cross-contamination between gas streams. Variable plate thickness, plate spacing, plate sizes, and air-flow patterns are designed to meet system requirements and fine-tune the system to maximize efficiency and cost savings. DPLs are most commonly used across the food processing industry in areas like bakery oven pre-heaters, indirect heating of sterilized air used for bottle drying at bottling plants, indirect heating of grain dryers, and pre-heating air for batch ovens.
Another style of air-to-air unit frequently utilized in the food industry is the vertical shell & tube heat exchanger. Cooling towers contain large tube diameters designed to cool air streams that have large amounts of particles. These towers help air control equipment to function more efficiently, and they recover heat that can be reused as building make-up air. This is a great system for facilities that use ovens, dryers, kiln cupolas, and incinerators with particulate exhaust emissions that need to be cooled or dried out before going into a more stringent, temperature-sensitive, particulate collection device. In food manufacturing, cooling towers are often used in conjunction with food dryers and feed dryers.
For food processors that demand the most heavy duty option, the shell & tube heat exchanger is the solution. This style of heat exchanger is designed for high temperatures and very dirty exhaust streams. It is ideal as a primary and secondary heat exchanger for various volatile organic compound abatement and fume incineration methods, including catalytic, thermal recuperative, and thermal regenerative incinerators.
PRE-heat Air-to-Air Innovation
Start your food processing industrial air innovation journey with PRE-heat. PRE-heat has been providing the highest quality air-to-air heat recovery units for over 40 years. Our knowledge of the industry has driven us to where we are today, creating improved shell and tube designs and improved plate designs all in-house.
See our food processing industry work in action in this case study for Marriott Walker Corporation, a powdered egg producer. We worked with Marriott Walker to design and deliver a custom plate heat exchanger that caused minimal disturbance to their process and used all of their existing process equipment to minimize costs.